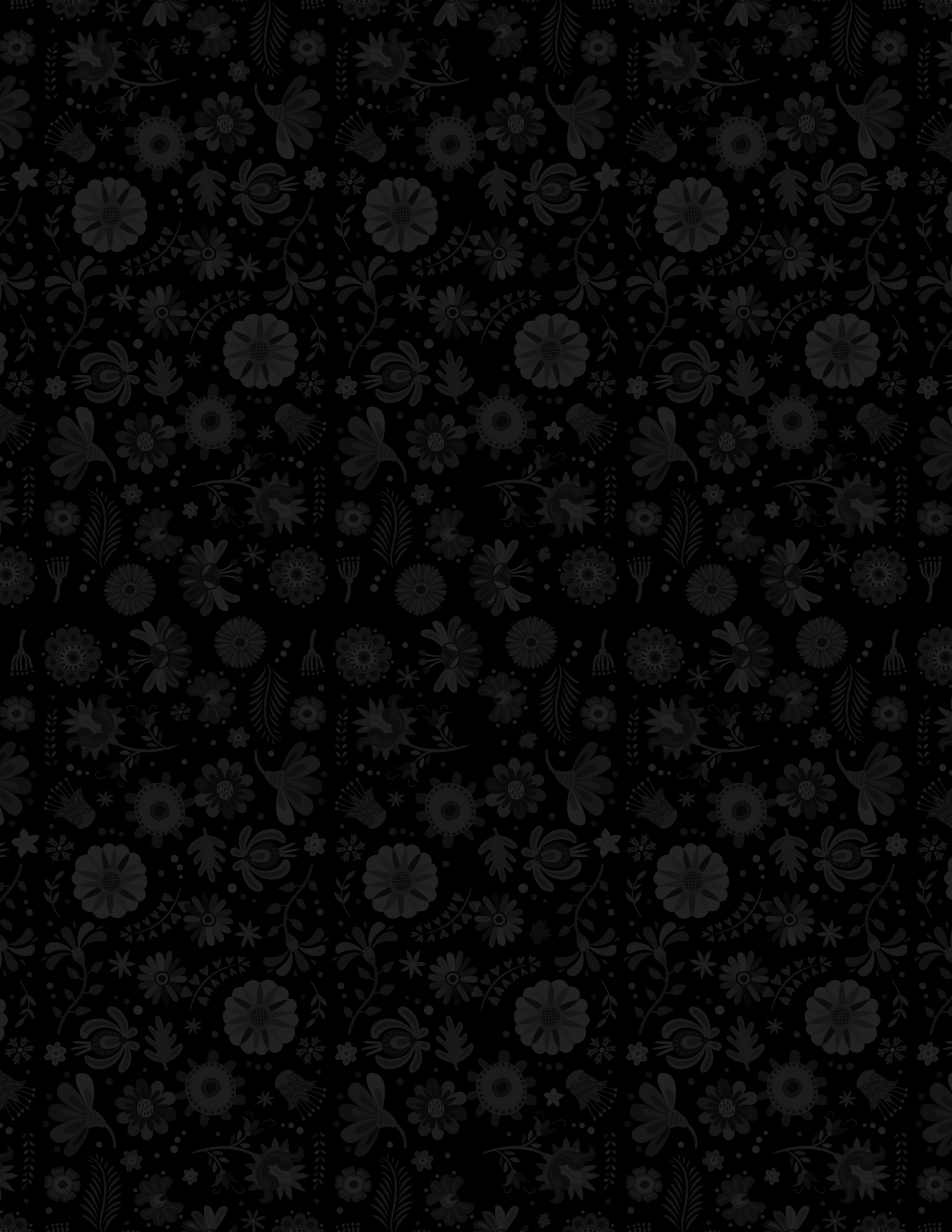
North America’s Smart Manufacturing Edge: Empowering Productivity Through Talent and Technology
By Eduardo Amaro, Regional Director, Mexico, Rockwell Automation
North America stands as a powerhouse of integrated manufacturing, where Canada, the United States, and Mexico seamlessly collaborate to produce complex, high-value goods—each nation contributing its unique strengths to a shared industrial engine. This collaborative process, known as co-manufacturing, sees products crossing borders multiple times before completion—a testament to the region’s deep logistical integration. Enabled in large part by the USMCA, this seamless movement of goods reflects a highly coordinated supply chain that leverages the strengths of each country.
One of the most compelling examples of regional collaboration is the production of an automobile—an intricate assembly of thousands of components sourced from across North America. Seat belts, airbags, and seats are manufactured in Mexico’s Bajío region; the chassis is built in Monterrey; the engine is produced in the United States; and the body is made from Canadian steel. The vehicle is painted in Guanajuato, before returning to the United States for final assembly. This is where the true strength of the bloc shines: in its geographic proximity, synchronized time zones, efficient logistics, standardized processes, and world-class quality standards. But perhaps most importantly, it’s the strategic use of talent across borders that makes this complex production chain not only possible, but globally competitive. North America thrives as a manufacturing bloc by recognizing and leveraging the unique advantages each country brings—creating a system that is greater than the sum of its parts.
In today’s fiercely competitive global landscape—where alternative manufacturing hubs offer aggressively low costs—preserving the profitability of the North American bloc is more critical than ever. At the heart of this challenge lie two deeply interconnected pillars: talent and technology. Together, they form the foundation of a resilient, future-ready manufacturing ecosystem capable of sustaining the region’s competitive edge.
Smart Manufacturing is emerging as a cornerstone of North America’s industrial competitiveness.
As defined by MESA International, Smart Manufacturing involves the intelligent, real-time orchestration and optimization of both physical and digital business processes—not only within factories, but across the entire value chain. This approach integrates automation, connectivity, and data-driven decision-making to ensure that resources and operations are continuously monitored, evaluated, and refined with maximum precision. By harnessing real-time data and advanced technologies, Smart Manufacturing empowers companies to respond swiftly to market demands, reduce waste, and enhance productivity—solidifying the region’s position in the global manufacturing arena.
Our latest report on the state of Smart Manufacturing reveals a striking trend: manufacturing companies increased their investment in smart technologies by an estimated 30% between 2023 and 2024. Leading the charge are technologies like Generative Artificial Intelligence (Gen AI), Digitalization, and Cybersecurity—each playing a critical role in boosting efficiency and mitigating operational risks. What’s particularly interesting is the clear, measurable return on these investments. These advanced capabilities are not just enhancements; they are becoming strategic differentiators in the global manufacturing race. When combined with the North American bloc’s inherent strengths—such as geographic proximity, synchronized logistics, and skilled talent—they position the region to lead the next era of industrial innovation.
To stay competitive in a rapidly evolving global market, manufacturers must prioritize three critical capabilities: process optimization and automation, agility to adapt to constant change, and scalability to support sustainable growth. Process optimization and automation drive efficiency, reduce waste, and enhance precision across operations. Agility enables companies to respond faster to shifting market demands, supply chain disruptions, and emerging opportunities. And scalability ensures that operations can expand seamlessly to meet growing business needs—without compromising profitability or quality.
Bridging the Skills Gap to Accelerate Innovation
One of the most critical enablers of successful technology adoption in manufacturing is talent. As smart manufacturing technologies become more deeply embedded in production processes, the demand for a workforce skilled in areas like automation, data analytics, AI, and cybersecurity continues to grow. For the second consecutive year, manufacturers across North America have identified the shortage of skilled labor as the primary barrier to outperforming global competitors. Closing this gap is no longer optional—it’s essential. Developing, attracting, and retaining talent with the right technical capabilities will determine how quickly and effectively companies can implement new technologies and scale their operations.
To bridge the widening skills gap, many industry leaders are turning to a dual strategy: adopting advanced technologies while simultaneously upskilling and reskilling their workforce. In fact, 94% of manufacturers report plans to either hire new talent or reassign existing employees to roles better aligned with smart manufacturing technologies.
At our 2024 edition of the North Capital Forum in Mexico City, it was highlighted that both Mexico and the United States rank among the top 10 countries globally in engineering talent production—graduating an average of 113,994 and 237,826 engineers annually, respectively. In Mexico, this number continues to rise steadily, driven by growing demand for roles tied to smart technologies, particularly in industrial hubs such as Nuevo León, Guanajuato, Jalisco, Coahuila, Querétaro, and the State of Mexico.
This robust talent pipeline strengthens the bloc’s competitive positioning. However, sustaining this momentum requires more than just producing engineers—it demands strategic efforts to develop, retain, and align this talent with the evolving needs of the industry. Ensuring that these professionals are equipped to lead in areas like automation, AI, and digital transformation is essential to unlocking the full potential of Smart Manufacturing across North America.
Advancing the development of engineering talent equipped for Smart Manufacturing is a shared responsibility—one that requires coordinated action from educational institutions, the private sector, and governments. Together, these stakeholders must work proactively to design and deliver comprehensive, future-focused training programs that evolve along technological advancements. Sustained investment in education, hands-on experiences, and continuous learning will be essential to ensure that the next generation of engineers is not only prepared to manage smart technologies, but to lead their innovation and implementation across the region.
Information Management: Fueling AI and Empowering Teams
The convergence of Information Technology (IT) and Operational Technology (OT) is accelerating the digital transformation of manufacturing across North America. Many companies are actively digitizing their operations—a shift that Rockwell Automation has championed in recent years by aligning digital maturity with measurable operational returns. Today’s automation solutions are more robust than ever, enhanced by a growing digital portfolio that includes tools like 3D process modeling, digital twins, and advanced analytics.
This digitalization is not just a trend—it’s a strategic necessity. The data generated on the production floor is the lifeblood of modern manufacturing, powering on-premise Artificial Intelligence algorithms that drive the shift from traditional automation to autonomous operations. These algorithms continuously analyze real-time data to make decisions and optimize processes with unprecedented speed and precision.
While many large manufacturers across the bloc have already adopted these technologies, there is a pressing need to support small and medium-sized enterprises (SMEs)—many of which are critical suppliers in the regional ecosystem—in accelerating their digital journey.
Currently, most organizations utilize less than half of the data they collect. The goal is to empower decision-makers with contextualized, real-time insights—supported by secure, integrated systems where cybersecurity is not an afterthought, but a foundational element. When data is effectively harnessed, it becomes a powerful tool not only for operational efficiency but also for empowering teams to make smarter, faster decisions.
Conclusion: A Shared Vision for a Smarter, Stronger Manufacturing Future
North America’s manufacturing strength lies not only in its integrated supply chains and geographic advantages, but in its ability to adapt, innovate, and collaborate. As Smart Manufacturing reshapes the global industrial landscape, the region has a unique opportunity to lead—powered by advanced technologies, a growing pool of engineering talent, and a shared commitment across sectors to continuous improvement.
To fully realize this potential, stakeholders must continue investing in digital transformation, workforce development, and cross-border collaboration. By aligning efforts across education, industry, and government, the North American bloc can build a resilient, future-ready manufacturing ecosystem—one that not only competes globally, but sets the standard for what’s possible in the age of intelligent industry.